飞机零件加工需要深度思考的步骤
更新时间:2025-04-27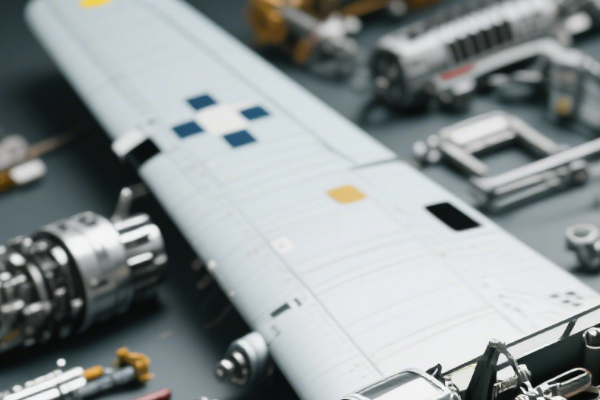
在航空制造领域,飞机零件加工是一项精密且复杂的系统工程,每一个步骤都直接影响飞机的安全性、可靠性与性能表现。从原材料的筛选到成品的交付,诸多环节都需要进行深度思考与审慎决策。这些深度思考不仅涉及技术层面的精准把控,更关乎对航空工业高标准、严要求的深刻理解与践行。
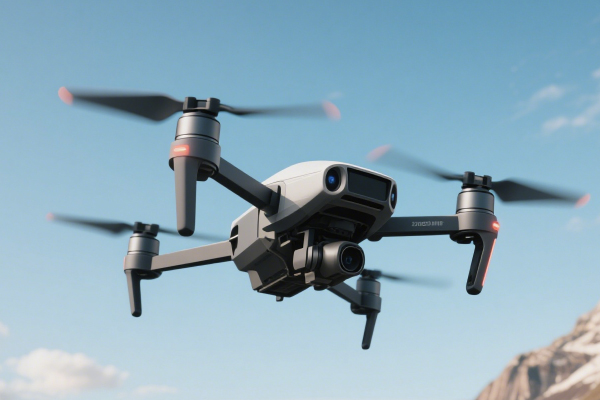
材料选择:性能与适用性的深度权衡
飞机零件对材料性能有着极高的要求,材料选择是加工的首要关键步骤,需要深度思考材料的各项性能指标与实际应用场景的适配性。首先,强度与重量的平衡是重中之重。飞机为了实现高效飞行,需要在保证结构强度的前提下尽可能减轻重量,以降低油耗、提升航程。例如,航空铝合金密度小、强度较高,广泛应用于飞机的机身框架、蒙皮等部件;钛合金虽然密度比铝合金略大,但具有高强度、耐高温、抗腐蚀等优异性能,常用于发动机压气机叶片、起落架等关键受力部件。在选择材料时,工程师需要根据零件的受力情况、工作环境等因素,精确计算材料所需的强度和刚度,同时评估材料的密度,在满足强度要求的基础上,选择最轻的材料方案。
其次,材料的耐腐蚀性与耐高温性能也不容忽视。飞机在高空飞行过程中,会面临极端的温度变化、高湿度以及大气中腐蚀性物质的侵蚀。对于长期暴露在外部环境的零件,如机翼蒙皮、机身外部结构件等,需要选择抗腐蚀性能良好的材料,并考虑是否需要进行表面处理来进一步增强防护能力。而对于发动机等高温部件,如涡轮叶片,必须选用能承受高温、抗氧化性能强的高温合金材料,以确保在高温燃气的冲击下,零件依然能保持稳定的性能。此外,材料的加工性能同样需要纳入考量,某些高性能材料虽然具备出色的使用性能,但加工难度极大,会显著增加加工成本和周期,因此需要在材料性能与加工可行性之间找到最佳平衡点。
工艺规划:精度与效率的综合考量
工艺规划是飞机零件加工的核心环节,直接决定了零件能否满足设计要求以及加工的成本和效率,这一过程需要深度思考多种因素的相互关系。首先,要根据零件的结构特点和精度要求选择合适的加工工艺。对于形状简单、精度要求相对较低的零件,如一些标准连接件,可以采用传统的机械加工方法,如车削、铣削等;而对于具有复杂曲面的零件,如航空发动机的涡轮叶片,五轴联动数控加工技术则更为合适,它能够通过精确控制刀具的运动轨迹,实现复杂曲面的高精度加工。同时,特种加工技术,如电火花加工、电解加工等,在加工高硬度、高熔点材料零件以及具有细微结构的零件时具有独特优势,也需要根据实际情况合理选用。
其次,工艺路线的优化至关重要。一个零件往往需要经过多道工序才能加工完成,合理安排工序顺序、确定各工序的加工余量和加工精度,能够有效提高加工效率和产品质量。例如,在加工大型飞机结构件时,通常会先进行粗加工去除大部分余量,然后再进行半精加工和精加工,逐步提高零件的精度和表面质量。在这个过程中,需要考虑各工序之间的加工余量分配是否合理,是否会因余量过大或过小影响加工精度和效率;同时,还需要考虑加工过程中的装夹方式和定位基准的选择,确保零件在加工过程中的稳定性和精度传递。此外,随着智能制造技术的发展,引入数字化工艺规划和仿真技术,可以在实际加工前对工艺方案进行模拟验证,提前发现潜在问题并进行优化,进一步提高工艺规划的科学性和准确性。
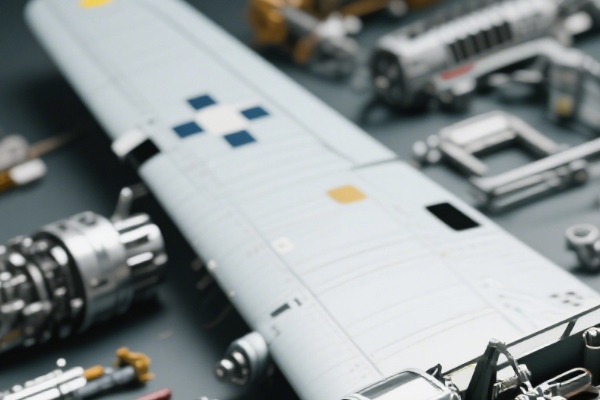
质量控制:全方位与全过程的严格把控
质量控制贯穿飞机零件加工的全过程,每一个环节都需要深度思考如何确保零件质量符合航空标准。首先,从原材料进厂检验开始,就要严格把控质量关。对原材料的化学成分、力学性能、金相组织等进行全面检测,确保其符合设计要求和相关标准。在加工过程中,要建立完善的质量监控体系,通过实时监测加工参数,如切削力、温度、振动等,及时发现加工过程中的异常情况,并采取相应的调整措施。例如,当切削力出现异常波动时,可能意味着刀具磨损或零件装夹出现问题,需要及时停机检查和处理,以避免产生废品。
其次,成品检验也是质量控制的关键环节。对于飞机零件,需要采用多种先进的检测技术进行全面检测。除了传统的尺寸测量、表面粗糙度检测外,还需要运用无损检测技术,如超声波检测、射线检测、涡流检测等,对零件内部的缺陷进行检测,确保零件不存在裂纹、气孔等影响使用性能的缺陷。同时,对于一些关键零件,还需要进行疲劳试验、强度试验等性能测试,以验证其在实际使用条件下的可靠性。此外,质量控制还需要建立完善的质量追溯体系,对每一个零件的加工过程进行详细记录,包括原材料批次、加工设备、操作人员、加工时间等信息,以便在出现质量问题时能够快速准确地追溯根源,采取有效的纠正和预防措施。
飞机零件加工的每一个步骤都蕴含着深度思考的必要性。从材料选择的性能权衡,到工艺规划的精度与效率考量,再到质量控制的全方位把控,只有在每一个环节都进行深入、细致的思考,综合考虑各种因素的影响,才能确保飞机零件的高质量加工,为航空工业的发展奠定坚实基础,保障飞机的安全飞行和卓越性能。