无人机零件加工:工艺、材料与挑战
更新时间:2025-04-15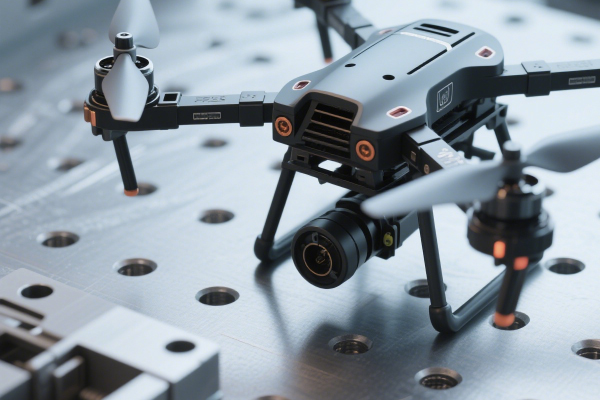
在科技飞速发展的当下,无人机凭借其独特优势,在航拍、物流配送、农业植保、测绘等众多领域得到了广泛应用。而无人机性能的优劣,很大程度上取决于其零件的加工质量。从材料选择到加工工艺的运用,每一个环节都至关重要。
材料选择:性能与需求的平衡
金属材料
铝合金因其出色的综合性能,在无人机零件加工中被广泛采用。它具有密度低、强度较高、加工性良好以及抗腐蚀性较强等特点。例如,无人机的机身框架部分使用铝合金,可在保证结构强度的同时减轻重量,有利于提高无人机的飞行性能和续航能力。像 6061 铝合金,经过适当的热处理后,能够满足无人机对零件强度和韧性的要求。
钛合金则凭借其高比强度、优异的耐腐蚀性和耐高温性能,在一些对性能要求极为苛刻的无人机零件加工中发挥着重要作用。例如,无人机发动机的某些关键部件,使用钛合金加工制造,能够承受高温、高压的恶劣工作环境,确保发动机稳定可靠地运行。不过,钛合金的加工难度较大,对加工设备和工艺要求较高。
复合材料
碳纤维复合材料在无人机领域的应用越来越广泛。它具有质量轻、强度大、抗疲劳性能好、耐腐蚀等诸多优点。将其用于无人机的机翼、机身等部件的加工,能够显著减轻无人机的重量,提升飞行效率和续航里程。研究表明,使用碳纤维复合材料制造无人机结构件,可实现减重 20%-30% 。例如,一些高端航拍无人机的机身采用碳纤维复合材料一体成型工艺制造,不仅使机身结构更加紧凑、坚固,还能有效降低风阻,提升飞行稳定性。
玻璃纤维增强塑料也是无人机零件加工常用的复合材料之一。它具备耐腐蚀、耐高低温、耐辐射、阻燃和抗老化等特性,有助于减轻飞行器重量,增加有效载荷,同时能实现美观的外观设计。在一些小型无人机的外壳、螺旋桨等零件加工中,玻璃纤维增强塑料应用较为普遍。
加工工艺:高精度与高效率的追求
数控加工
数控加工在无人机零件制造中占据着重要地位,对于生产高精度和复杂部件必不可少。通过计算机控制的铣床、车床等设备,能够精确地按照预设程序对零件进行加工,制造出具有精确公差的特定无人机结构件。
在无人机框架的加工中,数控加工发挥着关键作用。框架作为无人机的支撑结构,需要精确构造以确保适当的平衡和结构完整性。使用高性能复合材料,通过数控加工可制造出轻量化但坚固的框架。例如,采用五轴联动数控加工中心,能够在一次装夹中完成框架多个面的加工,大大提高了加工精度和效率,减少了装夹误差。
螺旋桨和旋翼作为无人机产生升力和推进力的关键部件,对其精度要求极高,以实现最佳空气动力学效率。数控加工能够确保螺旋桨和旋翼的叶片形状精确、平衡良好,这对于稳定飞行和高效动力使用至关重要。通过精确控制加工参数,如切削速度、进给量和切削深度等,能够保证叶片表面质量,降低气流阻力,提高螺旋桨的效率。
电机支架和齿轮等无人机配件同样需要加工到精确规格,以确保尺寸稳定。数控加工能够满足这些高精度要求,保证电机与支架的紧密配合,以及齿轮传动的平稳性,减少能量损耗,提高无人机的整体性能。
对于具有特定应用或独特设计的专用无人机,常常需要非标定制件。数控加工能够根据设计要求,制造出满足特殊工况的定制化无人机结构件,为无人机的个性化发展提供了有力支持。
注塑加工
精密注塑成型是一种在无人机制造中用于大量生产一致、高质量塑料零件的高效工艺。该工艺将熔融材料注入到具有所需零件形状的模具中,然后经过冷却、固化,最终得到成型的零件。
在无人机螺旋桨叶片的加工中,注塑成型工艺应用广泛。通过精心设计模具,可以制造出形状复杂、精度高的螺旋桨叶片,满足不同型号无人机对螺旋桨性能的要求。而且,注塑成型能够实现批量生产,有效降低生产成本。
无人机的外壳壳体和机身面板等零件也常常采用注塑加工工艺。模具可以设计成包含复杂的细节和形状,在制造过程中实现高度的定制化。同时,注塑成型生产的零件具有尺寸精度高、表面光洁度好等优点,能够提升无人机的整体外观质量和防护性能。
其他加工工艺
热压罐成型工艺在无人机复合材料零部件制造中较为常用。该工艺将复合材料毛坯用真空袋密封在模具上,放入热压罐中,在真空(或非真空)状态下,利用高温压缩气体对复合材料进行加热、加压固化成型。热压罐成型的优点在于罐内压力均匀,构件孔隙率较低、树脂含量均匀,模具相对简单,效率高,适合大面积复杂型面的蒙皮、壁板和壳体的成型。但该工艺也存在能耗高、辅助材料消耗大等缺点。
HP - RTM(高压树脂传递模塑)工艺是 RTM 工艺的优化升级,具有低成本、短周期、大批量、高质量生产等优势。它利用高压压力将树脂对冲混合,并注入到预先铺设有纤维增强材料和预置嵌件的真空密闭模具内,经树脂流动充模、浸渍、固化和脱模,获得复合材料制品。HP - RTM 工艺可生产尺寸公差较小、表面光洁度较好的小型复杂结构零件,实现复合材料零件的一致性。然而,其可制造零件尺寸有限,且由于树脂压力高和纤维压实松散,可能会冲刷分散纤维。
非热压罐成型技术是一种低成本复合材料成型技术,与热压罐成型工艺的主要区别在于材料成型时不需施加外压。该工艺在降低成本、制造超大型制件等方面具有明显优势,同时可确保均匀的树脂分布,并在较低的压力和温度下固化。成型模具要求相对热压罐成型模具大大降低,更容易掌控产品的质量。但该工艺生产效率相对较低、对材料性能要求较高。
模压成型工艺是将一定量预浸料放入到金属模具的对模模腔中,利用带热源的压机产生一定的温度和压力,使预浸料在模腔内受热软化、受压流动、充满模腔并固化成型。该工艺生产效率较高、制品尺寸准确、表面光洁,尤其对结构复杂的复合材料制品一般可一次成型,不会损坏复合材料制品性能。不过,模具设计与制造较为复杂,初次投入较大。
3D 打印技术在无人机零件加工中也逐渐崭露头角,它能够快速加工制造形状复杂的精密部件,无需模具即可实现个性化生产。在无人机复合材料零部件的生产中,3D 打印技术可以用于制造复杂结构的集成化部件,减少组装成本和时间。但该工艺存在打印速度慢、设备成本高等缺点。
加工挑战与应对策略
材料加工难点
铝合金虽然加工性较好,但在加工过程中容易出现变形问题。这是因为铝合金的热膨胀系数较大,在切削热的作用下,零件容易发生尺寸变化和形状变形。为解决这一问题,在加工过程中需要合理选择切削参数,如降低切削速度、增加进给量,以减少切削热的产生。同时,采用合适的冷却方式,如使用切削液进行充分冷却,能够有效控制零件的温度,减少变形。
钛合金的加工难度主要体现在其材料硬度高、切削力大、导热性差等方面。高硬度使得刀具磨损加剧,切削力大容易导致零件变形,而导热性差则使切削热集中在刀具刃口处,进一步缩短刀具寿命。应对这些问题,需要选用高性能的刀具材料,如硬质合金刀具,并采用特殊的刀具几何形状设计,以提高刀具的切削性能和耐用性。此外,优化切削工艺,采用低速、大进给的切削方式,配合强力冷却措施,能够有效降低切削温度,提高加工效率和质量。
碳纤维复合材料在加工过程中容易出现分层、纤维断裂等缺陷。这是由于碳纤维复合材料的各向异性和层状结构特点,在切削力的作用下,层间结合力容易受到破坏。为避免这些问题,需要采用专门的加工刀具,如金刚石涂层刀具,其锋利的刃口能够减少对纤维的损伤。同时,合理控制切削参数,降低切削力,采用分层切削、多道加工等工艺方法,能够有效减少分层和纤维断裂等缺陷的产生。
精度与质量控制
无人机零件对精度要求极高,尺寸公差通常要控制在极小的范围内。在加工过程中,由于设备精度、刀具磨损、工艺系统的热变形等因素的影响,容易导致零件尺寸偏差和形状误差。为确保精度,首先要选择高精度的加工设备,并定期进行维护和校准,保证设备的各项精度指标满足加工要求。其次,采用先进的刀具管理系统,实时监测刀具的磨损情况,及时更换磨损刀具,以保证加工过程中的切削精度。此外,通过建立精确的工艺模型,对加工过程中的热变形、力变形等因素进行预测和补偿,能够有效提高零件的加工精度。
在质量控制方面,除了保证尺寸精度和形状精度外,还需要关注零件的表面质量。零件表面的粗糙度、微观缺陷等会影响无人机的气动性能、疲劳寿命等。采用先进的表面检测技术,如光学显微镜、电子显微镜等,对加工后的零件表面进行检测,及时发现并处理表面缺陷。同时,优化加工工艺,选择合适的切削参数和加工路径,能够提高零件的表面质量。
无人机零件加工是一个融合了材料科学、机械制造技术、精密加工工艺等多学科知识的复杂领域。从材料的精心选择到各种加工工艺的巧妙运用,再到对加工过程中诸多挑战的有效应对,每一个环节都紧密相连,共同决定了无人机零件的质量和性能。随着科技的不断进步,新的材料和加工技术将不断涌现,为无人机零件加工带来更多的机遇和发展空间,推动无人机技术向更高水平迈进。
下一篇:无人机零件加工技术发展趋势剖析